CANBUS Technical
CAN was originally developed for passenger car applications. Nowadays, the majority of European carmakers are using CAN networks at least for the engine management. US carmakers have also decided to use CAN in power-engine applications, and the Asian companies have already started to develop CAN-based in-vehicle networks.
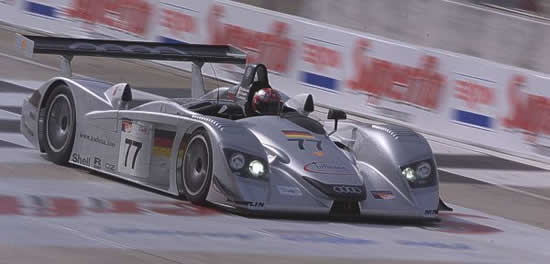
Audi R8, Le Mans winner, controlled by CAN.
Since 1992, Mercedes-Benz has been using CAN in their upper-class passenger cars. As a first step, the electronic control units taking care of the engine management were connected via CAN. In a second step, the control units needed for body electronics followed. Two physically separate CAN bus systems were implemented, connected via gateways. Other car manufacturers have followed the example of their peers from Stuttgart and now usually also implement two CAN networks in their passenger cars. After Volvo, Saab, Volkswagen and BMW, now also Renault and Fiat use CAN in their vehicles.
CAN networks used in engine management connect several ECUs (electronic control units). Mercedes-Benz was the first manufacturer who implemented CAN. Most of the other European automobile manufacturers also have implemented a CAN high-speed network (e.g. 500k bit/s) in their power-engine systems.
In addition, some passenger cars are equipped with CAN-based multiplex systems connecting body electronic ECUs. These networks running at lower data-rates, e.g. 125k bit/s. Most of them are using not the high-speed transceivers compliant with ISO 11898-2, but fault-tolerant transceivers compliant with ISO 11898-3. These multiplex networks link door and roof control units as well as lighting control units and seat control units.
A Brief Description of CAN
CAN is a serial bus system with multi-master capabilities, that is, all CAN nodes are able to transmit data and several CAN nodes can request the bus simultaneously. The serial bus system with real-time capabilities is the subject of the ISO 11898 international standard and covers the lowest two layers of the ISO/OSI reference model. In CAN networks there is no addressing of subscribers or stations in the conventional sense, but instead, prioritise messages are transmitted. A transmitter sends a message to all CAN nodes (broadcasting). Each node decides on the basis of the identifier received whether it should process the message or not. The identifier also determines the priority that the message enjoys in competition for bus access.
The relative simplicity of the CAN protocol means that very little cost and effort need to expended on personal training; the CAN chips interfaces make applications programming relatively simple. Introductory courses, function libraries, starter kits, host interfaces, I/O modules and tools are available from a variety of vendors permitting low-cost implementation of CAN networks.
Low-cost controller chips implementing the CAN data link layer protocol in silicon and permitting simple connection to microcontrollers have been available since 1989. Today there are more than about 50 CAN protocol controller chips from more than 15 manufacturers announced and available.
The use of CAN in most of European passenger cars and the decision by truck and off-road vehicle manufacturers for CAN guarantees the availability of CAN chips for more than 10 years. Other high volume markets, like domestic appliances and industrial control, also increase the CAN sales figures. Up to spring 1999 there are more than 150 million CAN nodes installed.
One of the outstanding features of the CAN protocol is its high transmission reliability. The CAN controller registers a stations error and evaluates it statistically in order to take appropriate measures. These may extend to disconnecting the CAN node producing the errors.
Each CAN message CAN transmit from 0 to 8 bytes of user information. Of course, you CAN transmit longer data information by using segmentation. The maximum transmission rate is specified as 1 Mbit/s. This value applies to networks up to 40 m. For longer distances the data rate must be reduced: for distances up to 500 m a speed of 125 kbit/s is possible, and for transmissions up to 1 km a data rate of 50 kbit/s is permitted.
Controller Area Network (CAN) is a serial bus system especially suited to interconnect smart devices to build smart systems or subsystems.
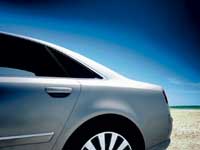
Audi A8 takes CANBUS to new levels.
The attributes of a Controller Area Network (CAN) are:
- the multi-master capabilities that allows to build smart and redundant systems without the need of a vulnerable master,
- the broadcast messaging that is the first piece of the guarantee for 100% data integrity as any device within the network is using the very same information,
- the sophisticated error detecting mechanism and the retransmission of faulty messages which is the second piece of the guarantee for 100% data integrity,
- the availability of more than 50 controllers from low-cost devices to high-end chips from more than 15 manufacturers announced and available,
- and the availability for the next 15 years as its use within the European automotive industry an the decision for CAN from the US and Japan automotive industry.
CAN networks can be used as an embedded communication system for microcontrollers as well as an open communication system for intelligent devices.
The CAN serial bus system, originally developed for use in automobiles, is increasingly being used in industrial as well as building automation, medical equipment and maritime electronics. If the requirements for passenger cars networks are compared with those for industrial field bus systems, the similarities are remarkable. In both cases some of the major requirements are: Low cost, the ability to function in a difficult electrical environment, a high degree of real-time capability and ease of use.
Some users, for example in the field of medical engineering, opted for CAN because they have to meet particulary stringent safety requirements. Similar problems are faced by manufacturers of other equipment with very high safety or reliability requirements (e. g. robots, lifts and transportation systems).
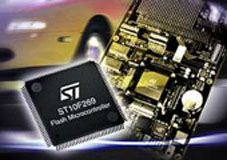
ST Microelectronics CAN controller IC.
The Need for Serial Communication in Vehicles
Many vehicles already have a large number of electronic control systems. The growth of automotive electronics is the result partly of the customer's wish for better safety and greater comfort and partly of the government's requirements for improved emission control and reduced fuel consumption. Control devices that meet these requirements have been in use for some time in the area of engine timing, gearbox and carburettor throttle control and in anti-block systems (ABS) and acceleration skid control (ASC).
The complexity of the functions implemented in these systems necessitates an exchange of data between them. With conventional systems, data is exchanged by means of dedicated signal lines, but this is becoming increasingly difficult and expensive as control functions become ever more complex. In the case of complex control systems (such as Motronic) in particular, the number of connections cannot be increased much further.
Moreover, a number of systems are being developed, which implement functions covering more than one control device. For instance, ASC requires the interplay of engine timing and carburettor control in order to reduce torque when drive wheel slippage occurs. Another example of functions spanning more than one control unit is electronic gearbox control, where ease of gear-changing can be improved by a brief adjustment to ignition timing.
If we also consider future developments aimed at overall vehicle optimization, it becomes necessary to overcome the limitations of conventional control device linkage. This can only be done by networking the system components using a serial data bus system. It was for this reason that Bosch developed the "Controller Area Network" (CAN), which has since been standardized internationally (ISO 11898) and has been "implemented in silicon" by several semiconductor manufacturers.
Using CAN, peer stations (controllers, sensors and actuators) are connected via a serial bus. The bus itself is a symmetric or asymmetric two wire circuit, which CAN be either screened or unscreened. The electrical parameters of the physical transmission are also specified in ISO 11898. Suitable bus driver chips are available from a number of manufacturers.
The CAN protocol, which corresponds to the data link layer in the ISO/OSI reference model, meets the real-time requirements of automotive applications. Unlike cable trees, the network protocol detects and corrects transmission errors caused by electromagnetic interference. Additional advantages of such a network are the easy configurability of the overall system and the possibility of central diagnosis. The purpose of using CAN in vehicles is to enable any station to communicate with any other without putting too great a load on the controller computer.
Use of the CAN in Vehicles
There are four main applications for serial communication in vehicles, each having different requirements and objectives.
Networking controllers for engine timing, transmission, chassis and brakes. The data rates are in the range - typical of real-time systems - of 200kBit/s to 1Mbit/s.
Networking components of chassis electronics and electronics, which make the vehicle more comfortable. Examples of such multiplex applications are lighting control, air-conditioning, central locking, and seat and mirror adjustment. Particular importance has to be attached here to the cost of the components and wiring requirements. Typical data rates are around 50kBit/s.
In the near future, serial communication will also be used in the field of mobile communication in order to link components such as car radios, car telephones, navigation aids etc. to a central, ergonomically designed control panel. The functions defined in the Prometheus project, such as vehicle-to-vehicle and vehicle-to-infrastructure communication will depend to a large extent on serial communication.
At present, CAN can be used for the first three applications, but for diagnosis the preferred solution is an interface according to ISO 9141.